In-House Repair & Logistics with ReSys
5
min read
Aug 3, 2017
Share:
The challenge
A repair and logistics company faced inefficiencies in tracking repair orders, managing spare parts, and ensuring timely delivery. Their previous system relied on disconnected tools, leading to delays, misplaced inventory, and poor workflow visibility. They needed an integrated solution to manage the entire repair lifecycle—from goods receipt to repair, shipment, and invoicing—while providing real-time insights into operations.
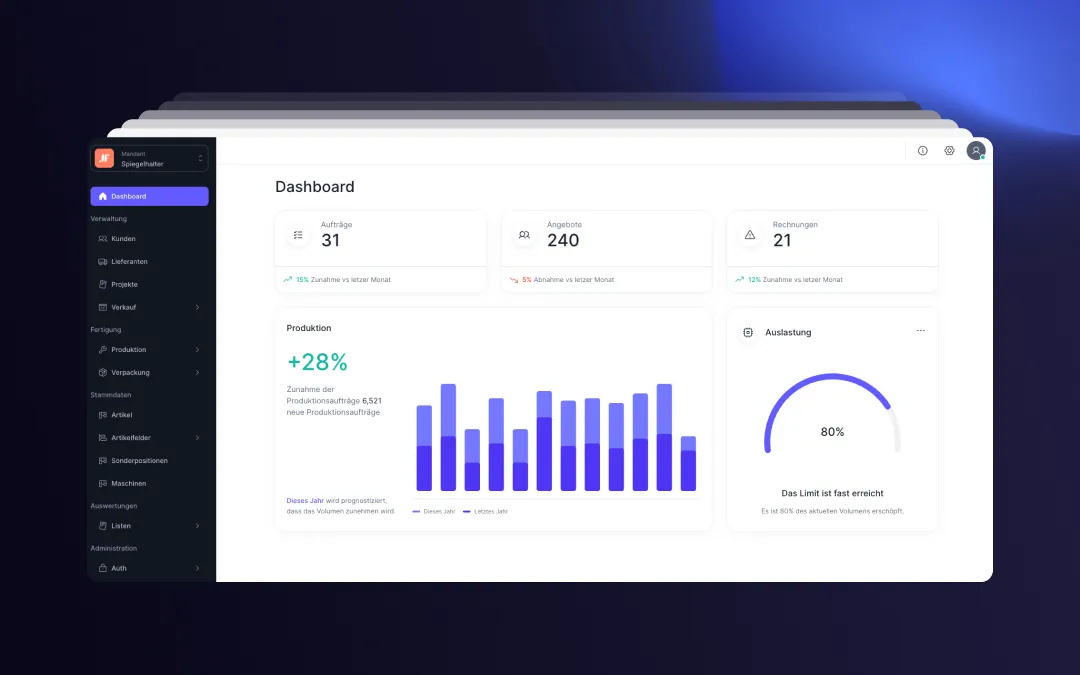
The challenge
Backend
Scalable backend built with ASP.NET, providing secure APIs, efficient data processing, and seamless integration with production systems.
Frontend
Custom user interface designed with Next.JS/React and TypeScript for easy navigation and interaction.
Integrations
APIs to connect with third-party tools, including email automation and payment systems.
Security
Robust encryption and security features to ensure the privacy and integrity of client data.
The challenge
40%
Faster Repair Turnaround
Automated workflows reduced processing times and optimized repair scheduling.
30%
Improved Inventory Management
Better tracking of spare parts minimized losses and ensured availability when needed.
25%
More Efficient Logistics
Optimized shipment tracking reduced delivery errors and improved turnaround times.
🛠️ End-to-End Repair Tracking
Every step, from goods receipt to repair completion, is tracked in real-time, reducing errors and ensuring full visibility. Teams can monitor progress, quickly resolve issues, and maintain workflow efficiency.
📑 Automated Order & Workflow Management
Repair orders are assigned automatically and tracked through each stage, reducing manual effort. This speeds up processing, minimizes errors, and improves overall operational efficiency.
✅ Smart Spare Parts Inventory
Real-time stock updates prevent shortages and ensure parts are always available. This reduces repair delays, optimizes inventory usage, and minimizes unnecessary stockpiling.
📆 Optimized Scheduling & Resource Allocation
Intelligent scheduling assigns repairs based on priority, technician availability, and part readiness. This helps reduce downtime, improve efficiency, and maximize resource utilization.
🚛 Integrated Logistics & Shipment Tracking
Shipments of repaired items are tracked seamlessly from dispatch to delivery, reducing errors. This improves accuracy, minimizes lost shipments, and ensures on-time returns.
📊 Real-Time Reporting & Performance Insights
Live analytics provide insights into repair times, costs, and logistics performance. Managers can make data-driven decisions to optimize operations and improve service efficiency.
By implementing ReSys, the company reduced repair turnaround by 40%, improved inventory tracking by 30%, and optimized logistics efficiency by 25%. The centralized system streamlined repair and logistics operations, enhancing productivity, accuracy, and customer satisfaction.